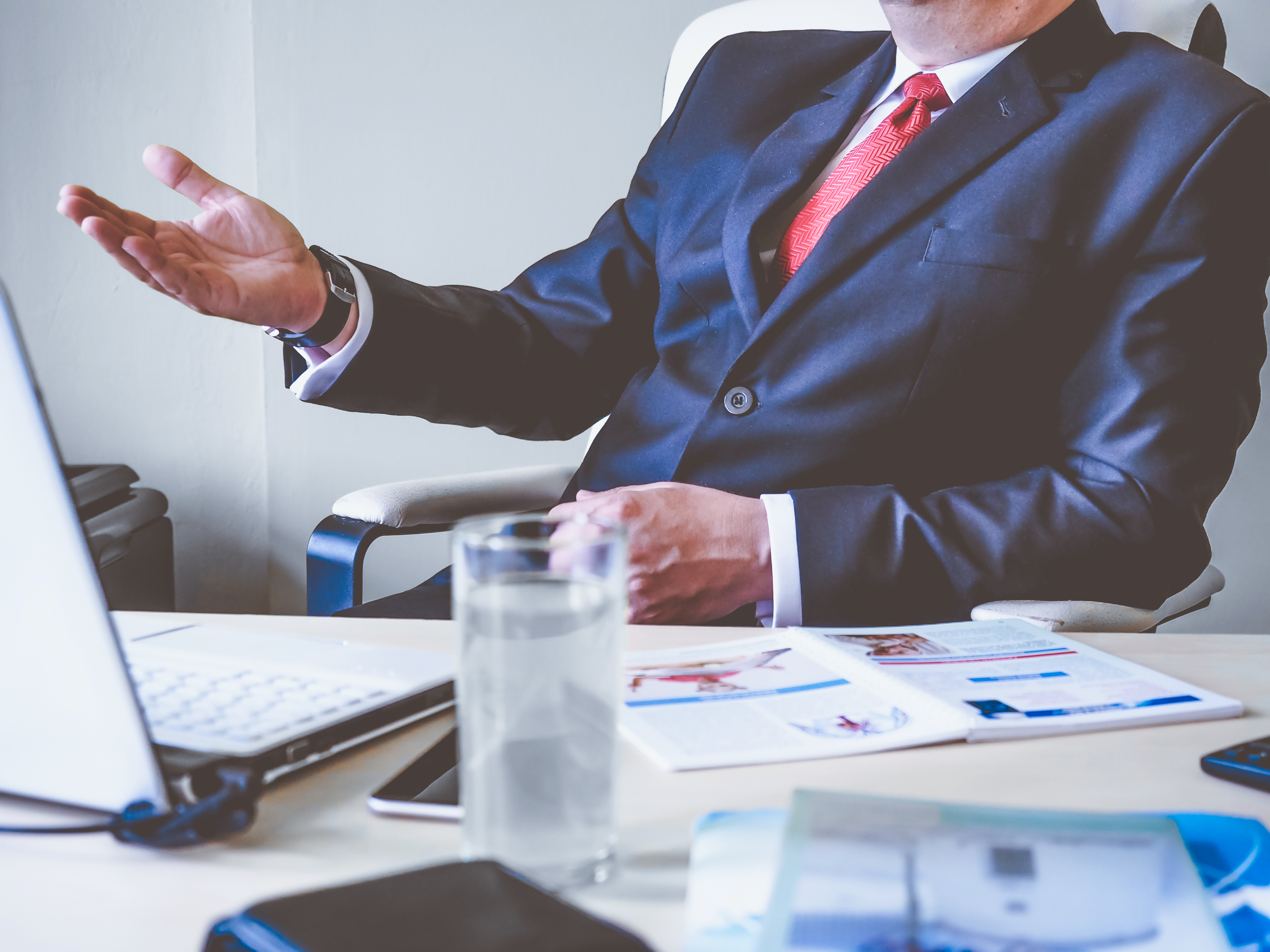
Lean Management und ERP Systeme
Autor:
Robert Friedemann, B.Eng., MBA
Lean Management, ein fast schon mythischer Name im industriellen Umfeld, ist seit fast 30 Jahren ein wichtiges, nicht wegzudenkendes Managementsystem, bei dem die effiziente Gestaltung von Produktion, Produktionsentwicklung und die Prozessoptimierung einem kontinuierlichen Verbesserungsprozess und einem schlanken Management unterliegen.
Die Geschichte des Lean Management hat seine Wurzeln im äußerst strukturierten Toyota Production System (TPS)[1] der 1950er Jahre. In den späten 1950er und den 1960er Jahren wurde Total Productive Maintenance (TPM) und in den 1980er das deutlich mehr prozessorientierte Total Quality Management (TQM) entwickelt. Diese Ansätze hatten zu Beginn (TPS) die Aufgabe, die Prozesse in der Produktion so effizient wie möglich zu gestalten. Während in den 1950er und 1960er Techniken wie passives oder aktives Lot-Tracking, CIM-Anlagenkopplungen, ERP- oder MES-Systeme noch nicht bekannt waren, mussten die Effizientesten der Welt, zum damaligen Zeitpunkt war das der japanische Automobilbauer Toyota, mechanische und logistische Methoden entwickeln, mit denen es möglich war einen hohen Durchsatz bei gleichzeitig geringer Bestands- und Umlaufmenge sowie höchster Qualität zu entwickeln.
So fanden TPS-Methoden wie ChakuChaku[2], 5S, Hanedashi oder Hejunka[3] ihren Platz in der Fertigung. Das Chaku-Chaku-Prinzip beschreibt den Schwerpunkt der Tätigkeiten des beschäftigten Personals auf dem Be- und Entladen im U-Layout von automatisierten Montagestationen (Hanedashi) sowie dem Transport der Werkstücke. Die Montage mit derartigen Systemen gestattet eine Skalierung der Leistungserstellung durch den variablen Einsatz von Personal. Mit der 5S-Methodik (Sortieren, Systematisieren, Säubern, Standardisieren, Selbstdisziplin) verfolgt man das Ziel, die am Arbeitsplatz nicht wertschöpfenden Tätigkeiten, die Verschwendung, zu eliminieren oder auf ein Minimum zu reduzieren. Als Hejunka, auch Nivellierung, wird die Einteilung der in einem Zyklus zu produzierenden Produkte in Einzelrationen bezeichnet. Wird die Tagesmenge in weitere Teilmengen (Taktzeiten) zerlegt, so wird von Glättung gesprochen. All diese Methoden halfen Toyota dabei, sich in Qualität und Leistung von der Konkurrenz abzusetzen
Über die folgenden Jahre sind weitere betriebliche Funktionen wie das TPM (Total Productive Maintenance) hinzugekommen. Ziel war es, die Tätigkeiten der Instandhaltung zu optimieren. Dabei wurden die Hauptziele der 100%igen Anlagenverfügbarkeit, der präventiven Instandhaltung, der Rüstzeitoptimierung und des Null-Fehler-Prinzips optimiert. Die produzierenden und begleitenden Bereiche hatten somit eine große Palette an Methoden und Techniken zur Auswahl, die für die Optimierung und Effizienzsteigerung der Bereiche eingesetzt werden konnten. Bekannte Methoden des TPM[4] sind SMED, Qualitätszirkel und LCIA.
Die stetige Weiterentwicklung der Methodik und die globale Ausbreitung des Buches „The machine that changed the world“[5] waren die Begründung des Lean Management. Während die vorgelagerten Entwicklungsstufen ihren Schwerpunkt in allen Belangen der Fertigung hatten, setzte das Lean Management hier keine ausschließlichen Akzente mehr. Lean Management wird als allgemeiner Managementansatz gesehen, der in allen betrieblichen Funktionen Einzug halten sollte. So waren nun auch administrative Bereiche gefragt, den Ablauf ihrer Tätigkeit zu optimieren. Methoden wie das First in First Out Prinzip vermieden nicht nur in der Fertigung die Überlagerung von Bauteilen, sondern halfen auch der Verwaltung, Aufgaben termingerecht und in Folge zu erledigen. Wurden vorher Arbeitsplätze in der Fertigung mit der 5S-Methode „gereinigt“, wird nun die 5S-Methode auch als 5S@Office eingesetzt. Der Siegeszug des Begriffes Lean Management startete in den Vereinigten Staaten und wurde in den späten 1980ern und frühen 1990ern dann auch in Europa mehr und mehr bekannt. Seit dieser Zeit hält der Vormarsch des Lean Managements an und immer mehr Industriebereiche und auch das Dienstleistungsgewerbe[6] setzen das „schlanke“ Management ein um die eigene Firma zu optimieren. In den letzten Jahren ist ein vermehrter Trend des Einsatzes von Lean Management im Gesundheitssektor festzustellen.[7][8][9] Der Erfolgszug wird weiter gehen und immer mehr Firmen jeder Branche werden sich dem Thema Lean öffnen.
Während sich die Geschichte des Lean Managements weiter und weiter entwickelte, begann auch die industrielle Revolution, oft unter den Namen Industrie 1.0, Industrie 2.0, Industrie 3.0 und Industrie 4.0 geprägt. Während Industrie 1.0 die mechanische Entwicklung im 18. Jahrhundert beschreibt und Industrie 2.0 die elektronische Revolution zu Beginn und Mitte des 20. Jahrhunderts, entwickelte sich in den 1970ern Industrie 3.0[10], die beginnende IT-Automatisierung, parallel zu den Methodiken um das Lean Management.
Während Lean in den frühen Jahren weitgehend auf die informationstechnische Entwicklung verzichtete war ein wichtiger Teil der dritten industriellen Revolution die Entwicklung von Enterprise Ressource Planning Systems. So soll das grundlegende Ziel eines ERP Systems sein, die Ressourcen aller Unternehmensbereiche effizient und effektiv zu managen, zu beeinflussen und auszugestalten.[11] Beim Vergleich der Intention von ERP und Lean sind einige, hier nur ausgewählte, kooperierende Ziele festzustellen. Dazu zählen:
- effiziente Ressourcennutzung
- keine Verschwendung
- Layoutoptimierung
- Durchlaufzeitoptimierung
- Minimierung des Verbrauchsmaterials
- Optimierung des Umlaufbestandes
- Minimierung der Lager
- a.
So zeigt sich ein gewisser Synergieeffekt der in Fachmedien kontrovers diskutiert wird. Zu Grunde liegt, dass die Einführung von ERP-Systemen in nur 39% der Fälle erfolgreich funktioniert, jedes fünfte Projekt fehlschlägt und rund 64% aller Projekte im zeitlichen Umfang zu knapp bemessen sind.[12] Dies zeigt, dass bereits bei der Einführung von ERP-Systemen ein deutliches Verbesserungspotential gegeben ist. So können Methoden der Organisation wie FiFo, Just in Time, Just in Sequence, Kanban, Poka Yoke, Muda, Muri oder auch 5S bereits bei der Einrichtung des ERP-Systems berücksichtigt werden.[13] Für Kunden ergeben sich daraus zwei Vorteile: der Prozessfluss wird deutlich effizienter gestaltet und die Sicherheit sowie Nachverfolgbarkeit der Daten im System kann gesteigert werden.
Eine umfangreiche Forschung der Fachhochschule Kufstein unter der Leitung von Prof. Dr. Martin Adam zeigt, dass knapp die Hälfte der ERP-Hersteller in Ihrer Software Lean-Management unterstützen, jedoch nur ein Bruchteil der Anwender die Funktionalitäten nutzen.[14] Dr. Daryl Powell beschreibt in seiner PhD-Thesis den Zusammenhang zwischen Lean und ERP als Paradoxon. Als Beispiel führt er hier z.B. die kontroversen Ziele fixe Leadtime bei ERP im Gegensatz zu One-Piece-Flow und Just-in-Time an. In Bezug auf diese Symantik ist der Einbezug von Lean in ERP Systeme wiederum nicht möglich. Weiterhin zeigt er in seiner Arbeit auf, dass sich seit den 1990ern der Anspruch an die Fertigungsbetriebe weiter geändert hat und Ansprüche des Lean Managements in Bezug auf eine erfolgreiche Unternehmung abgebildet werden müssen, moderne ERP-Systeme unterstützen dies.[15]
Lean Management wird seit vielen Jahren erfolgreich angewendet und hat viele Befürworter als auch einige Gegner. Ähnliches lässt sich unter Bezug der ausgewählten Quellen auch für die Anwendung von Lean Management Methoden bei der Implementierung und dem Einsatz von ERP-Systemen zeigen. Grundsätzlich bietet der Lean-Baukasten viele Methoden, die bei der Einführung als auch im kontinuierlichen Betrieb des ERP-Systems unterstützen können. Allein die effiziente Layoutgestaltung und Abbildung einer schlanken Produktion in einem ERP-System verringert den Aufwand und bedeutet weniger Implementierungsarbeit. Moderne Fertigungen mit einer Vielzahl an Produkten und Fertigungsschritten können keine Economie of Scale abbilden und sind gezwungen die vorhandenen Systeme variabel auszugestalten, zu rüsten und verfügbar zu machen. Das ERP-System muss diese Funktionen unterstützen und mit einem optimalen MES-System interagieren, um die Wertschöpfungskette zu optimieren.
Kontakt:
SIS Consulting GmbH
Tel. +43 512 890080
info@sis-consulting.com
Über SIS Consulting GmbH:
Die SIS Consulting GmbH begleitet als unabhängige und neutrale Unternehmensberatung Unternehmen im deutschsprachigen Raum. Das Dienstleistungsangebot umfasst die Felder Prozessmanagement, Enterprise Systems und Franchising. Die SIS Consulting veröffentlicht jährlich das ERP Booklet, welches eine schnelle Orientierung und eine solide Vergleichbarkeit von ERP Systemen und Anbietern ermöglicht.
[1] Taiichi Ohno: Das Toyota-Produktionssystem, Campus-Verlag, 2005
[2] Gorecki/Pautsch: Lean Management, Pocket Power, Hanser Verlag, 3. Auflage, München, 2013
[3] Franz J. Brunner: Japanische Erfolgskonzepte; 2. überarbeitete Auflage; HANSER-Verlag, München
[4] Gorecki/Pautsch: Lean Management, Pocket Power, Hanser Verlag, 3. Auflage, München, 2013
[5] Womack, Jones, Roos. (1990). The Machine that Changed the World. Simon & Schuster. LaJolla. USA.
[6] Philipp Stüer: Gestaltung industrieller Dienstleistungen nach Lean-Prinzipien, Apprimus, 2015
[7] Robinson, S. T., Kirsch, J. R. (2015). Lean Strategies in the Operating Room. Anesthesiology Clinics, vol. 33, iss. 4. Portland. USA. pp. 713-730.
[8] D’Andreamatteoa, A., Iannia, L., Legab, F., Sargiacomo, M. (2015). Lean in healthcare: A comprehensive review. In Health Policy, vol. 119, iss. 9. Elsevier. Ireland. pp. 1197-1209.
[9] Hicks, C., McGovern, T., Prior, G., Smith, I. (2015). Applying lean principles to the design of healthcare facilities. International Journal of Production Economics, vol. 170, iss. B, pp. 677-686
[10] Vom “Web 2.0” zur “Industrie 4.0”: Wo blieb das “3.0”?: http://www.viernull-magazin,de, 2016
[11] Was ist ein ERP-System: http://www.erp-system.de, 2016
[12] Standisch Group, 2000
[13] Lean und ERP – Synergie oder Widerspruch?: http://www.leanmagazin.de, 2016
[14] Prof. Dr. Martin Adam: ERP-Systeme im Lean Management, GITO Verlag, Berlin, 2014
[15] Dr. Daryl Powell: Investigating ERP support for Lean Production, Norges teknisk-naturvitenskapelige universitet, Department of Productions and Quality Engineering, 2012
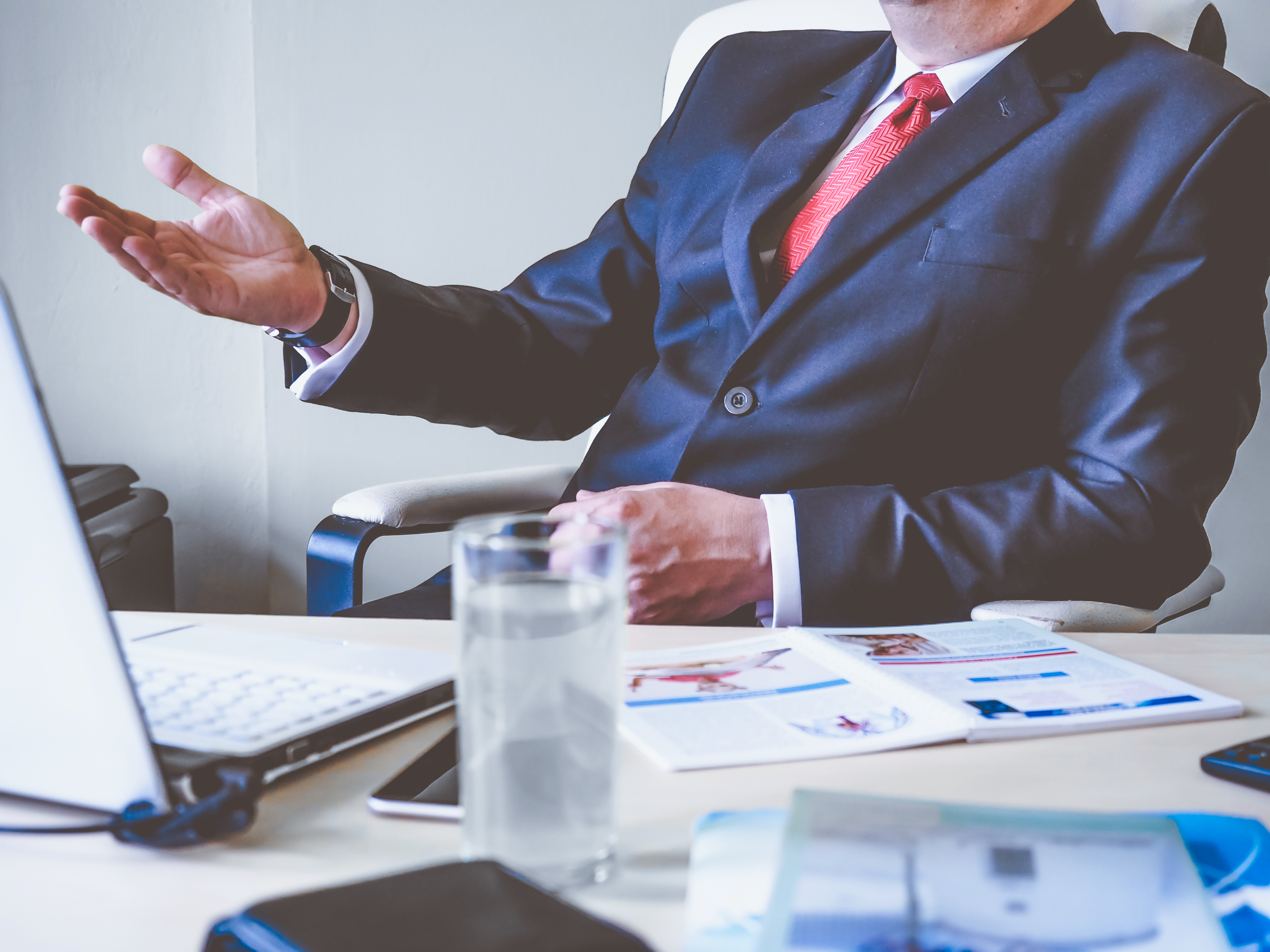
Lean Management, ein fast schon mythischer Name im industriellen Umfeld, ist seit fast 30 Jahren ein wichtiges, nicht wegzudenkendes Managementsystem, bei dem die effiziente Gestaltung von Produktion, Produktionsentwicklung und die Prozessoptimierung einem kontinuierlichen Verbesserungsprozess und einem schlanken Management unterliegen. Ob und welche Synergieeffekte sich mit ERP-Systemen ergeben lesen sie im Fachartikel von Robert Friedemann.
Den Fachartikel können Sie hier herunterladen: